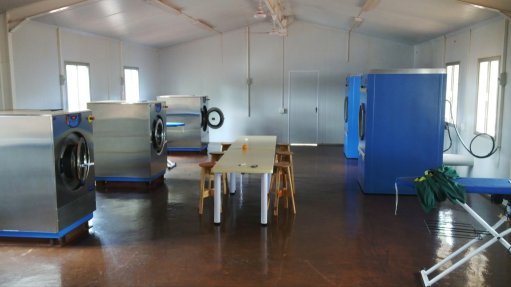
SPARE PARTS Implementing and maintaining an inventory of critical spare parts will reduce unnecessary downtime, thereby reducing costs and saving time
Mass accommodation and remote-site catering, laundry and hospitality solutions provider Ascot Site Solutions aims to ensure employee comfortability by reducing the risk of accommodation-related equipment breakdowns.
A remote site can have its own “frustrations”, but Ascot’s maintenance strategy allows for assisting mine-site accommodation maintenance teams by providing troubleshooting advice and solutions, explains Ascot Site Solutions MD Rhett Bellamy.
The company can provide mine-site accommodation solutions, including kitchen, laundry and refrigeration equipment and services, for mine camps of up to 16 000 mineworkers.
In addition to Ascot’s dedicated team of experienced technicians, who can be contacted through video calls to assist and, consequently, save on their having to make costly trips, the company also provides training programmes to easily identify, troubleshoot and maintain mine-site accommodation equipment.
Remote mine sites will often not have the correct spare parts – if any all – for essential accommodation-related equipment; any breakdowns will, therefore, severely impact on the daily operations of facilities.
The implementation of a spare parts management system is, thus, necessary, adds Bellamy, who notes that maintaining an inventory of critical spare parts will reduce unnecessary downtime, thereby reducing costs and saving time.
In addition to skills development and spare parts management, maintenance teams can conduct routine inspections and service mine-site accommodation equipment to identify any signs of wear and tear or to identify looming malfunctions.
Ascot suggests that the servicing of all mine-site accommodation equipment be done at least every third to fourth month to ensure equipment uptime and efficient operability.
Case in Point
A large mine, in Lesotho, had frequent breakdowns, as well as the wear and tear of laundry equipment at its central laundry facility, which resulted in costly repairs, downtime and an overall inconvenience to staff.
Ascot implemented a comprehensive maintenance strategy focused on preventative maintenance, staff training and the provision of critical spare parts on site, Bellamy tells Mining Weekly.
This was followed up by a schedule of regular maintenance checks and equipment servicing every four months.
Bellamy notes that, in the past two years since this strategy was implemented, the company has not received call-outs to the site to do emergency repair work.
He notes that, amid logistical challenges in Africa, there will always be situations where a large number of people need to be housed in close proximity to their places of work.
“Therefore, Ascot will continue to offer the same high-level service to its customers while continuing to look for growth opportunities,” concludes Bellamy.