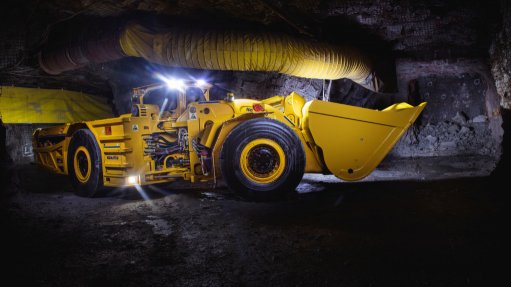
LIMITED SPACE The Komatsu WX07 LHD has been engineered for demanding underground environments, designed for small, narrow-vein applications with limited manoeuvring space
In an environment where cost control and remaining competitive and financially viable are constant challenges for operators of underground hard-rock mines, mobile machinery manufacturer Komatsu reports that employing new technology is the logical starting point for making every aspect of a mine’s daily operations more efficient and cost effective.
To support the local market with these challenges, Komatsu recently launched its range of underground hard-rock equipment in Southern Africa.
Highlighting that load-haul-dumpers (LHDs) are the mainstay of any underground operation, Komatsu reports that its WX07 LHD is engineered for the most demanding mining environments.
The WX07 LHD is a heavy-duty, 7 t diesel-powered machine designed for especially small, narrow-vein mining applications with limited manoeuvring space.
The loader is one of three products that signal Komatsu’s entry into African underground hard-rock mining – a move that will support the large-scale extraction of minerals required to facilitate the world’s transition to a low-carbon future.
“The low-waste, small footprint ethos of narrow-vein mining aligns perfectly with the environmental, social and governance- [ESG-] conscious direction in which the South African mining sector is heading,” states Komatsu senior technical sales representative Jaime Harripersad.
“The introduction of the Komatsu WX07 loader allows small and narrow-vein mines promising advancements in technology, safety, productivity and operator comfort,” he adds.
Komatsu reports that the LHD has achieved much success in North and South America, as well as parts of Central Asia, for its “superior performance”.
Industry comparisons show that the WX07 has a breakout force up to 10% greater than other machines in its class, along with a 15% advantage in operating speed, when fully loaded, according to Komatsu.
Equipment Drawcards
The key benefits of the WX07 LHD include a robust, fully enclosed cab and intuitive controls to protect operators from overhead hazards and the harmful effects of occupational dust and noise.
With double curved glass for 360° visibility and unobstructed sightlines, as well as ample headroom for ease of entry and exit, the cab has been designed with safety and comfort in mind.
The control panel for the WX07 is designed to be easy to use and informative. All the data and information an operator would need to perform tasks, such as autogenerated diagnostic measurements, adjustments and live data readouts, are readily accessible on a sleek touch screen control panel.
Another important safety feature is an open-door interlock, which automatically activates the brakes, and deactivates the boom, bucket and steering function, as soon as the cab door is opened.
In terms of drivetrain, the WX07 employs a Z-link design, which, according to Komatsu, enables optimum penetration and rapid bucket filling, giving it the fastest boom cycle in its class.
A new and simplified powertrain also elevates productivity and reduces costs.
The powertrain consists of a Cummins Tier 3, 215 hp engine and is paired with a Dana electronic transmission and C3000 torque converter. This is a combination that delivers high levels of productivity and lower operating costs.
Time spent refuelling is also reduced with the WXO7’s 243 ℓ fuel tank, which significantly increases operating hours and reduces refuelling downtime.
Ground-level maintenance is another user-friendly advantage. To provide easy serviceability within the confines of narrow vein mining operations, it ensures that most vital components are well within reach.
On-board data monitoring and management also result in improved servicing, troubleshooting, training and performance.