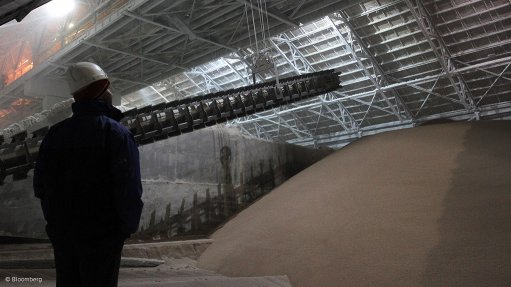
The main supplier of igneous phosphate to the EU was Russia, which is no longer viable
Photo by: Bloomberg
Norwegian mining and exploration company Norge Mineraler chairperson John Vergopoulos says the discovery of a large igneous phosphate deposit sets the company apart as a key supplier of raw critical materials for the European Union’s (EU’s) energy transition.
Norge has identified a geological system of 3.4-billion tonnes of Joint Ore Reserves Committee-compliant resources in Norway, confirmed by consulting firm SRK. The company is also sitting on a significant vanadium resource, as well as titanium.
Phosphate rock is used to produce yellow phosphorous, also known as P4, through a furnace process and, further downstream, phosphorous chemicals used in agriculture, mining, and aviation, in addition to lithium iron phosphate (LFP) battery electrolyte used in electric vehicles (EVs). Through a separate flow sheet, a wet processing procedure on phosphate rock is used to make phosphoric acid, and eventually various phosphate fertilisers and LFP cathode, Vergopoulos explains.
“There is not a complete understanding of the importance of igneous phosphate compared to sedimentary phosphate. Sedimentary is the most common form with major deposits in North Africa, Kazakhstan and China, however, given that it is formed over millennia with the accumulation of marine material, it contains impurities including carbonates, silicates and other trace elements. Igneous phosphate, which accounts for 5% of global supply, however, is formed through the crystallisation of magmatic material without the associated impurities of sedimentary rock. The Norge deposit at Eigersund has the highest purity phosphate in the world at over 96%,” Vergopoulos tells Mining Weekly.
He notes that the higher purity translates to a more straightforward and efficient extraction process, leading to purer phosphoric acid.
The impurities in sedimentary phosphate, such as heavy metals, organic matter and other contaminants, can complicate the phosphoric acid production process and may require additional purification steps, which can be costly and energy-intensive.
“There is a huge growth area in the market for phosphorous and there is no new supply coming into the market. The other major problem is that phosphorous imports bring high levels of carbon dioxide emissions into the supply chains,” Vergopoulos explains.
When it comes to the production of LFP batteries, impurities in phosphoric acid can negatively affect their performance and lifespan. Pure phosphoric acid ensures that the electrolyte solution maintains its desired properties, leading to optimal battery performance and longevity in EVs.
Contaminants in phosphoric acid can also pose safety risks, such as increased corrosion or chemical reactions within the battery.
In general, purifying phosphoric acid derived from sedimentary phosphate deposits involves additional chemical treatments and energy-intensive processes, leading to increased environmental impact. Using igneous phosphate with inherently higher purity reduces the need for such treatments, contributing to a more sustainable battery manufacturing process.
“For the markets we're looking to address, sedimentary phosphate is not applicable. They need high purity igneous phosphate for LFP batteries,” Vergopoulos explains.
He says the contaminated slag produced by sedimentary phosphorous production will be a major problem for production in Europe and will not get past the regulatory barriers.
“The producers in Europe need igneous phosphate owing to the EU regulatory environment, as the sedimentary phosphate produces contaminated gypsum and contaminated raffinate that they can't deal with. They can't store it and they can't sell it. Therefore, they need igneous phosphate,” Vergopoulos says.
He notes that, previously, the main supplier of igneous phosphate to the EU was Russia.
“This is now no longer an option, given the embargo on Russian material so they have to look further afield. This is a problem, not just for supply now, but also to meet the demand growth in future. This is why the integrated approach that we're taking has been met so positively by the EU and by various governments, because it's a looming supply time bomb that's just not being addressed anywhere,” Vergopoulos says.
The company is undertaking a prefeasibility study, which is due to be published in the third quarter.
Vergopoulos says Norge is already in conversation with various European governments and potential strategic partners to determine the optimum downstream processing flowsheet for production of phosphorous to meet the expected demand growth in the market.
The aim is to establish a new integrated value chain of critical raw materials in the region.
“The situation right now in Europe regarding the energy transition is that it will be fuelled by critical raw materials such as vanadium and phosphorous, which is 100% imported into the EU. We're completely reliant on other areas of the world, most notably Russia and China. This is a fundamental problem to supply chain security,” Vergopoulos says.
Norge is looking to not just meet supply chain needs, but also to deliver a net-zero solution to the EU critical raw materials supply chain.
“What we're looking to do is to build integrated supply chains enabling security of supply and net-zero products throughout the value chain,” he says.
Part of this process will include the development of one of the first fully electrified mines in Europe, using renewable power to produce zero carbon critical raw materials to a local supply constrained market in Europe. This will be achieved through a partnership with ABB.
The two companies announced in August last year that they were teaming up to deliver a front-end engineering design study for the upstream mine production.
ABB and Norge are exploring the entire electrification of the future mining and downstream operations, including control system options to provide a complete overview of the mine and integrate advanced operations.
The ABB study aims to address electrification, automation and digitalisation to improve sustainability, cost-efficiency and productivity at the mine from the outset, with a focus on low energy consumption.