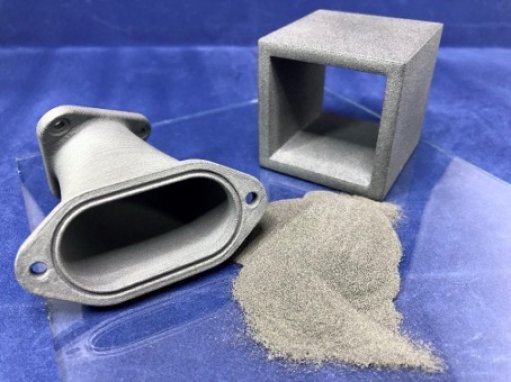
Lehvos LUVOSINT powder and laser sintered parts
A need has been identified for inexpensive but extremely flame-retardant plastic powders with low smoke toxicity that can be processed safely on available laser sintering machines.
Requirements for the flame retardancy of plastics vary from application to application, but are especially difficult for railway components. The relevant fire protection standard EN 45545 describes different risk classes, with the highest class required for trains that travel underground. This is because passengers on an underground train cannot easily exit and move away from a danger zone, and need time to get past the train to safety in a tunnel. In addition to flames and heat, flue gas is an additional hazard and the prevention of the immediate toxic effect of the smoke in the cramped conditions of the train and tunnel is also critical.
The availability of safe plastics for such applications is limited and if the components are manufactured using 3D printing, the only option thus far has been expensive high-performance polymers in filament printing. Where laser sintering is the preferred 3D printing technology, the process is even more difficult, expensive and requires rare high-temperature machines. High temperatures of up to 390°C in the printers put a strain on the powder, which results in high refresh rates and high powder consumption. In addition, high-performance materials from the top of the plastic pyramid are highly resistant to breakdown by chemical or mechanical load. This makes the production of fine powders for laser sintering very difficult and not economically viable.
SIEMENS Mobility says it has developed the basics for applicable flame-retardant plastic powders which have been transferred to a new laser sintering material in close cooperation with the LEHVOSS Group.
The LUVOSINT PPS 9268 BK product is based on a polyphenylene sulfide (PPS). Although PPS is intrinsically flame-resistant, it does not inherently meet the requirements of the highest hazard classes of EN 45545. This was achieved by the additional modification of the polymer. In laser sintering, the PPS powder is said to offer a comfortable process window at part bed temperatures of around 250 °C. The inherently high flowability of PPS supports the pressure-free sintering of the powder into dense components during laser sintering. These show typical PPS mechanics with high rigidity and strength. Components do not absorb moisture and are therefore dimensionally stable. PPS is also chemically and thermally very stable, enabling used part bed powders to be completely recycled.
The material is coloured black and can be processed with CO2 lasers as well as fibre lasers, which enable speed without loss of precision, increasing productivity for industrial production. All these factors contribute to significantly reduce costs for EN 45545-compliant components using laser sintering.
SIEMENS Mobility says that its declaration of conformity shows that printed components from LUVOSINT PPS 9268 BK meet the requirement sets R1HL3, R7HL3 and R17HL3 according to DIN EN 45545-2 with a cost of material comparable to that of conventional polyamide powder for laser sintering.
The use of the LUVOSINT PPS 9268 BK is not limited to railway applications. The material also meets the flame retardancy requirements placed on components for use in aircraft and buses. In addition, an HDT A of 196 °C enables its use in high temperatures. PPS is also said to be particularly suitable for applications with requirements for chemical resistance.