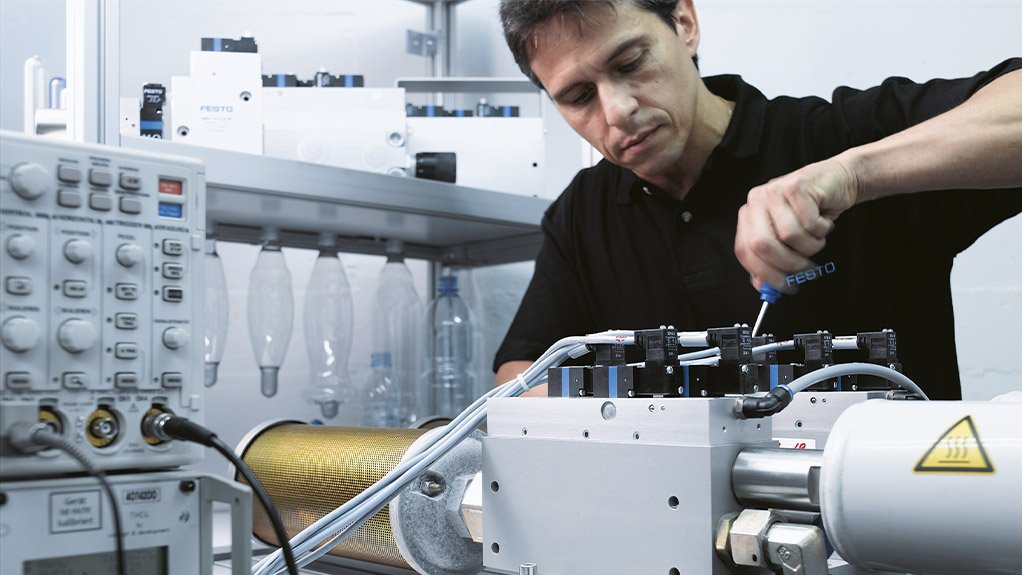
Thanks to high-pressure pneumatics, stretch blow moulding machines achieve an output per blow moulding station of between 1,000 and nearly 3,000 PET bottles per hour. The key to this success is precise control using valves, and valve blocks and proper compressed air preparation. These are supplied by Festo, along with global services, from design engineering tools to operation.
For over ten years, the global player in automation technology has been developing a comprehensive range of components for high-pressure pneumatics up to 40 bar for manufacturing PET bottles using blow moulding for linear and rotary machines. The development engineers at the company’s headquarters in Esslingen use their own high-pressure laboratory where the pneumatic products are qualified. The products are manufactured and tested in the Festo Scharnhausen Technology Plant, located near Esslingen, in accordance with the Pressure Equipment Directive. You can rest assured that you get all the appropriate approvals and the quality feature “Made in Germany”.
Machine learning for monitoring
Festo developers are working on digitalised high-pressure applications for monitoring and other smart components. The Festo AX machine learning software plays its part as it monitors and analyses machine data. It also helps to optimise production processes and save valuable resources, ensuring greater sustainability and energy efficiency.
The data collected during monitoring can be analysed via dashboards and the condition of individual valves or, depending on the scope, even entire systems can be tracked. It is not just machine conditions that can be monitored; it also makes it possible to carry out predictive maintenance.
Customised solutions for high-pressure pneumatics
The comprehensive standard range of high-pressure pneumatic products with air preparation for small to large flow rates, with modular service unit components, regulators, filters, switch-on and switch-off valves and proportional valves leaves nothing to be desired when it comes to the development of stretch blow moulding machines. In addition to the standard product range, Festo develops customised service units and valve blocks for individual machine solutions.
As a full-service provider of pneumatic and electric automation, the company can also set the entire production line in motion, from pre-forming to palletising. Depending on the application area, Festo produces valve terminals, control cabinets, drives, control blocks, high-pressure pneumatic products or system solutions.
At the end of 2021, Festo received the “Customer Centric” award from the Sidel Group. One of the most important manufacturers of beverage filling systems thus acknowledged the tireless commitment of the sales, production, supply chain and development teams.