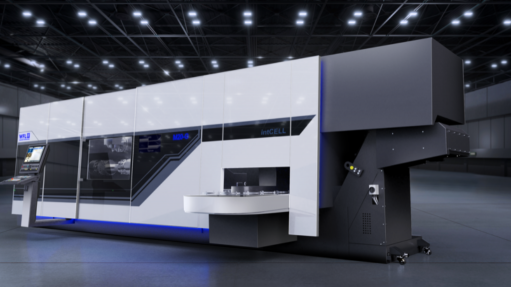
UNIT FEATURES
The new M20 MILLTURN has a turning machining unit with B-axis and automatic tool change on the lower system.
Photo by: Design Tech
Austrian mechanical engineer WFL Millturn Technologies’ latest development has enabled the company to manufacture the complete machining of chuck parts with a diameter of 2 000 mm.
The complete machining of chuck parts for the aerospace industry is one of the core competencies of WFL Millturn Technologies, which noted that it has been able to gain “quite an advantage over the years” for chuck parts where the diameters are often the same as or considerably larger than the workpiece length.
“When it comes to the machining of chuck parts, most production specialists immediately think of vertical machining. It's true that the vertical machining of chuck parts, particularly ring- and disc-shaped parts, offers a few advantages,” the company commented in a press release.
However, it highlighted the convenient loading and unloading of workpieces, and that chip removal in vertical machining is often problematic, whereby chips and cooling lubricant often remain in the workpiece and disrupt the machining process.
This is where horizontal machining creates considerably better conditions, WFL noted.
The most important issues, when it comes to producing complex chuck parts, usually relate to both the machining itself and to the loading and alignment of the parts in the clamping device, the company said.
It explained that the vertical setup and alignment of the parts are also important conditions of horizontal machining.
WFL has therefore embraced this concept and challenge and is developing innovative complete solutions for the horizontal complete machining of chuck parts, which has many strengths in comparison with vertical machining, the company noted.
Based on a high-precision, rigid and fully variable clamping system, clamping devices like workpiece-specific pallets, power chucks, clamping mandrels and collet chucks can be manually or automatically changed as required, the company explained.
With this solution, the workpiece is clamped and aligned on the clamping pallet on a vertical external clamping table or setup station.
The setup station is equipped with the exact same interface as the headstock in the form of a stable, short taper mounting with a high degree of repeat accuracy. The clamping device including the workpiece can be changed automatically.
Alternatively, when using power chucks, the workpieces can be changed directly into the chuck by the robot and the workpieces can also be transferred to the counter spindle, thus enabling full six-sided machining, according to WFL.
“This automation solution from WFL enables extremely stable clamping with a high degree of repeat accuracy. This concept also practically eliminates the need for clamping device setup times in the machine,” the company said.
It added that the horizontal machining of power chucks offers numerous benefits, including simple and efficient clamping of workpieces and increased efficiency through setups concurrent with machining.
This method allows for maximum flexibility, as parts can be prepared and stored simultaneously outside the machine.
Horizontal orientation enhances chip flow and productivity is further boosted by four-axis machining capabilities using a turning-boring-milling unit or a tool turret. Additionally, features such as the transfer of chuck parts to the counter spindle enable machining on the rear side.
The system accommodates flexible switches between pallets and hydraulic power chucks and supports the use of prismatic tool systems on virtually all WFL machines, facilitating the use of special or heavy internal machining tools.
Depending on the machine model, additional tool carriers such as turrets are used in addition to the turning-drilling-milling unit. This second processing unit is located on the lower system.
“Machining can therefore take place simultaneously on both turning spindles or four-axis on one spindle at a time. A special feature of all WFL machines is the integrated measuring probe, which is used for both horizontal and vertical machining and ensures advantages in the quality of the components,” WFL explained.
With the new M20 MILLTURN, specifically, the lower system also features a turning-machining unit with B-axis and automatic tool change.
Particularly when metal-cutting demanding materials, such as stainless steel, titanium, heat-resistant superalloys, among others, with a high degree of tool wear, WFL said it is possible to work fully automatically without interruption for very long periods of time.
“Thanks to the external tool magazine, a larger tool stock is available. The unproductive downtime required to retrofit the turret tools is eliminated,” WFL said.
A production increase of up to 80% can thereby be achieved during turning, the company added, noting that the combination of these advantages results in a significant increase in productivity when machining chuck parts.
The external setup and alignment of workpieces at the setup station, combined with the automatic swapping of clamping devices and workpieces by robots, substantially reduces machining time. The addition of a second single tool holder eliminates downtimes for setting up workpieces or tools, streamlining the entire process.