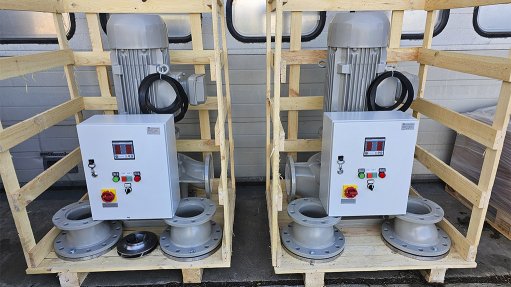
The intricate logistics of fuel loading and unloading in marine transport demands efficiency and reliability at every turn.
Central to this process are cargo pumps, the unsung heroes facilitating seamless loading and unloading of fluids onto vessels. From heavy fuel oil to chemicals like methanol, these pumps ensure the safe transfer of diverse liquids into a ship's cargo hold.
In its latest project, North Ridge Pumps was tasked with the transfer of D2 diesel from cargo tanks to shore, where the marine client faced a pressing challenge: discharge the entire fuel load within a tight 10-hour window. Moreover, they sought a pump solution capable of sustaining continuous operation for up to 14 hours at a time, streamlining the loading and unloading process into a single, efficient visit.
Client Challenges
Facing constraints with their current setup, the client grappled with the challenge of integrating a new pump into their existing 200 mm pipework. They required a resolution whereby a solution could be installed without the need for extensive pipework modifications. Durability and ease of maintenance were also a design priority as the client was based in Guyana, where sourcing parts and materials for repairs can be problematic.
Moreover, operating from Guyana, they emphasised their need for durability and ease of maintenance, being acutely aware of the logistical hurdles in sourcing materials and parts locally.
There are often several considerations when looking to specify a pump onboard a vessel for cargo loading / offloading:
Design: Space is at a premium aboard any ship, with vertical height often being more available than horizontal space. The layout of this vessel meant that horizontal space was extremely limited meaning a vertical inline pump with a smaller footprint was the best solution.
Operation: Vessels have limited time when docked to discharge their cargo. Any delays can lead to costly demurrage charges for ship owners, so pumps must be able to operate efficiently and continuously for several hours.
Safety: A light fuel pump was required as this project involved the transfer of D2 diesel. Gasoil is classified as a flammable liquid (H226), so both pump and motor in this case required ATEX certification.
Contaminated D2 diesel can cause serious safety concerns for the end user such as reduced engine performance and total engine failure, so the transfer system also had to minimise the risk of fuel contamination.
The Solution
North Ridge Pumps supplied two ATEX-certified VXEN vertical inline centrifugal pumps, equipped with Siemens IE3 ATEX motors. This system delivered the client’s requirements in several ways:
Low initial investment costs
The vertical inline pumps had simplified piping arrangements and a smaller footprint, which served to simplify the installation process and reduce installation costs. Also, the pump design chosen was one that involved a simplified centrifugal design, which was only possible owing to the fuel’s low viscosity.
Ease of maintenance
The VXEN vertical inline centrifugal pump has a back pull-out design that allows the motor to be removed while the pump is still connected to the pipework. This reduces the downtime required for the pump to be serviced/maintained as internal parts are easily accessible without disconnection of the pump from the pipework.
Operating times and efficiency
North Ridge Pumps was able to specify the pumps for a flow rate of just over 3 000 ℓ/min, enabling the tank to be emptied in just over six hours – four hours ahead of the target time – reducing the likelihood of demurrage and ensuring the vessel usage was maximised. The Siemens IE3 ATEX motors were rated for continuous operation, exceeding the brief requirements for operation of up to 14 h/d.
Profit margins
Inaccurate fuel transfer measurements can affect the customer’s bottom line and one way this can be protected is through accurate metering. North Ridge Pumps supplied two oval gear meters with a 24 V local display which were accurate to within 0.5%, thus enabling accurate measurement of the amounts transferred. This ensured that the customer could account and bill for all fuel transferred.
Adaptation to existing infrastructure
The pumps were supplied with counter flanges that transitioned from DN150 on the pumps to DN200 mm. This matched the onsite pipework and ensured a seamless integration without the need for replacing any of the existing infrastructure. The counter flanges conformed to EN 1092-2 / PN 16 for steel and stainless steel casings.
Compact design
The vertical centrifugal configuration of the pumps offered a compact footprint, with the motor affixed atop the pump, and straight-line alignment with the pipes at both inlet and outlet. This was crucial as horizontal space aboard the vessel was limited.
Durability
The pumps were designed with durability in mind. The pump casing was made from ductile iron, enhancing the pump's ability to withstand high pressures (up to 100 m) without damage. In addition, the pumps had low net positive suction head requirements, reducing the risk of dips in performance, and of damage from cavitation and wear and tear. Both the centrifugal pump and motor had independent shafts for added robustness. This means that only the pump shaft would need to be replaced in the event of a breakdown, and if the motor should ever fail, that could be easily sourced locally on short lead times.
These diesel transfer pumps were also fitted with bronze wear rings which help to maintain operational clearances and efficient operation, while simultaneously protecting the impeller and the main pump casing from wear. Additionally, a lantern bracket was installed between the pump and the motor, creating a space to protect the motor from fluid ingress in the case of a seal failure. These features all served to prolong the overall life of the pump and reduce the costs associated with repairs and downtime.
Safety
Both the VNEX vertical inline pump and the Siemens IE3 motor were ATEX certified, being safe for use in explosive environments and the handling of flammable liquids. Anti-static paint was used on the pump and motor to prevent sparks and the build-up of static electricity inside the pump itself – a critical safety measure when handling flammable substances like gasoil. The pumps were also designed to deliver safe high-volume transfers, avoiding the risk of the tank becoming over-pressurised if overfilled.
North Ridge Pumps is an independent manufacturer of pumps. It is not tied to a single pump technology, so it can select the most appropriate pump for any application. Its solutions are not limited to pumps – it can also provide flowmeters and complete pump kits where required.
If you have a pump you need specifying for a fuel transfer application, contact us on +44 (0) 1773 302 660 or email sales@northridgepumps.com to see how we can help.
https://www.northridgepumps.com/p_1243_vxen-vertical-inline-centrifugal-pump