Electric shovels receive 50 000-hour service
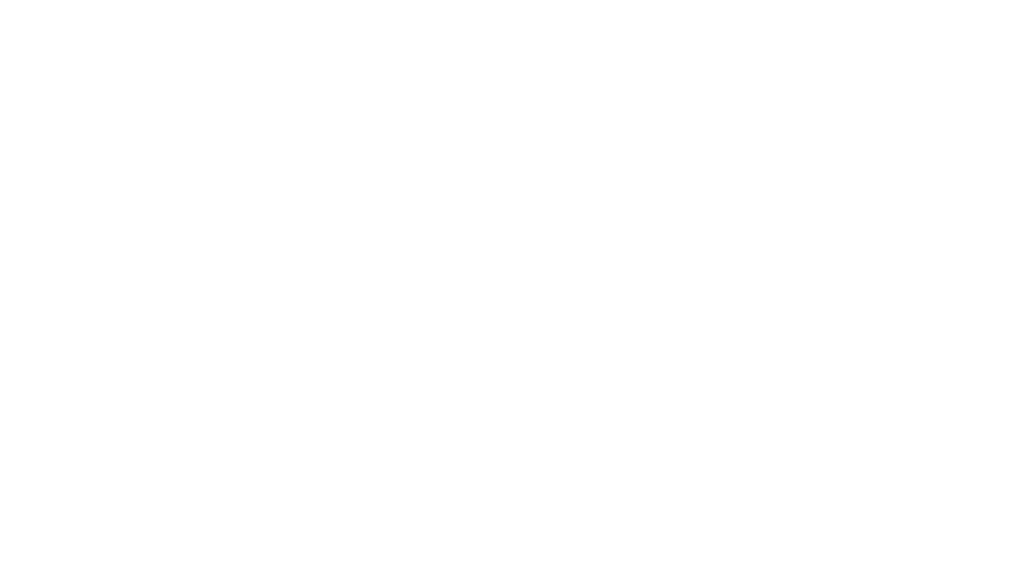

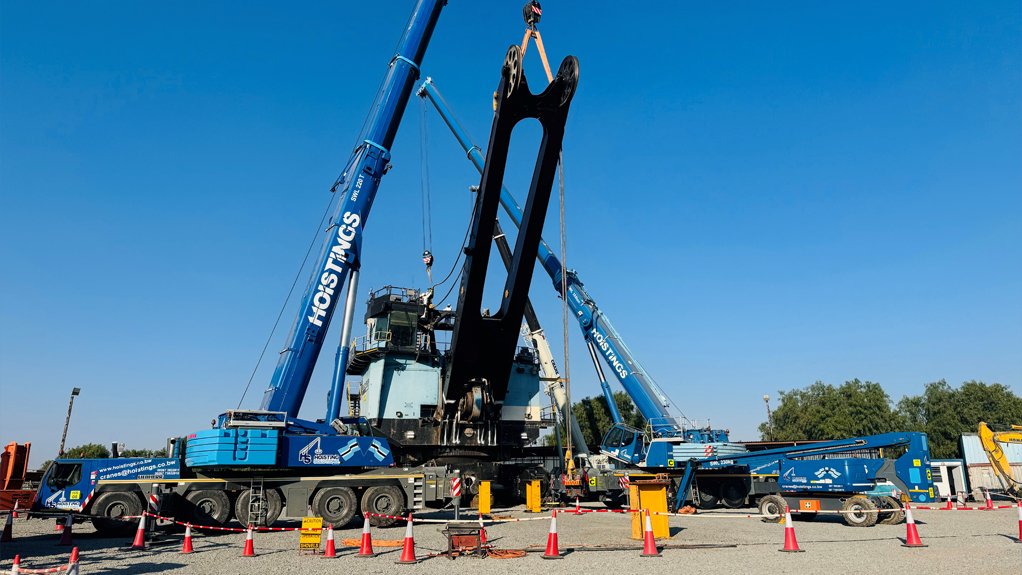
MAJOR SERVICE The 50 000-hour component replacement project is intended to bring heavy-wear components back into a serviceable state that is in line with original equipment manufacturer specification
HEAVY UNDERTAKING Such is the size of the electric rope shovels used at the Jwaneng mine that two cranes can be seen here removing components to be refurbished as part of the major service procedure
A 50 000-hour component replacement project on one of the large electric rope shovels owned and operated by original-equipment manufacturer (OEM) Barloworld Equipment (BWE) Botswana is going to plan, with recommissioning of the equipment expected in September.
The project is being undertaken by diamond producer Debswana, which employs Bucyrus electric rope shovels of the 212 model at its Jwaneng operation, for which BWE Botswana provides parts and maintenance services.
The project, scheduled to take 120 days, will employ 120 staff, as well as subject matter experts – mostly BWE employees – at its peak.
The 50 000-hour service is required as once the electric rope shovels reach an operational life span of 50 000 hours, their major components are deemed to have exceeded their life expectancy and require replacement according to the life-cycle cost of the machine and OEM guidelines, explains Jwaneng key account manager and project lead Odirile Pitswe.
“A machine runs for a specific time following which it must undergo a planned component replacement,” he says.
To date, repairs on the car body through non-destructive testing and parts machining, as well as the installation of the side frames and the tandem lifting boom, have been completed.
Welding the repaired components is also required, including the boom, car body and side frames.
The swing girders have been successfully removed and the boom lowered while maintaining a zero injuries, first-aid-incident-free and high-potential-incident-free record, highlights Pitswe.
The four months set aside for the planned component replacement was influenced by the requirement for on-site crack repairs and milling of the car body, as well as the general condition of other components.
“The benefits of this 50 000-hour planned component replacement will ensure that the electric rope shovel complies with all safety requirements and will extend the asset life of the equipment and improve performance and reliability,” he adds.
In addition, the maintenance of such critical equipment will reduce mining production interruptions resulting from breakdowns and will promote better budget management regarding costs planning and allocation.
“Debswana, on the other hand, ensures that there is a greater return on investment from its assets, and production remains at its peak,” says Pitswe.
Bringing in the Big Guns
The components for the electric rope shovel – including the hoist, swing, crowd and propel machinery – are brought in from all over the world, including South Africa, the US and China.
Pitswe lauds the involvement of BWE Botswana regarding its sourcing and supplying of parts and logistics, as well as managing the use of parts to support production machines during unplanned breakdowns, from start to finish.
BWE has also been crucial in managing project scope creep and in communicating all unplanned tasks to the client while generating a revised management process.
“BWE has been instrumental in maintaining the quality control and quality assurance of the project by ensuring all components are dispatched for repairs and are done to global OEM Caterpillar specifications, using Caterpillar salvage guidelines.”
He adds that despite the potential challenges, BWE remains grateful for the chance to showcase its capabilities in delivering the best customer experience safely, which is its primary objective for this project.
“There is a considerable amount of planning and execution involved in a project of this magnitude, with millions of Pula being earmarked for it by Debswana,” concludes Pitswe.
Comments
Press Office
Announcements
What's On
Subscribe to improve your user experience...
Option 1 (equivalent of R125 a month):
Receive a weekly copy of Creamer Media's Engineering News & Mining Weekly magazine
(print copy for those in South Africa and e-magazine for those outside of South Africa)
Receive daily email newsletters
Access to full search results
Access archive of magazine back copies
Access to Projects in Progress
Access to ONE Research Report of your choice in PDF format
Option 2 (equivalent of R375 a month):
All benefits from Option 1
PLUS
Access to Creamer Media's Research Channel Africa for ALL Research Reports, in PDF format, on various industrial and mining sectors
including Electricity; Water; Energy Transition; Hydrogen; Roads, Rail and Ports; Coal; Gold; Platinum; Battery Metals; etc.
Already a subscriber?
Forgotten your password?
Receive weekly copy of Creamer Media's Engineering News & Mining Weekly magazine (print copy for those in South Africa and e-magazine for those outside of South Africa)
➕
Recieve daily email newsletters
➕
Access to full search results
➕
Access archive of magazine back copies
➕
Access to Projects in Progress
➕
Access to ONE Research Report of your choice in PDF format
RESEARCH CHANNEL AFRICA
R4500 (equivalent of R375 a month)
SUBSCRIBEAll benefits from Option 1
➕
Access to Creamer Media's Research Channel Africa for ALL Research Reports on various industrial and mining sectors, in PDF format, including on:
Electricity
➕
Water
➕
Energy Transition
➕
Hydrogen
➕
Roads, Rail and Ports
➕
Coal
➕
Gold
➕
Platinum
➕
Battery Metals
➕
etc.
Receive all benefits from Option 1 or Option 2 delivered to numerous people at your company
➕
Multiple User names and Passwords for simultaneous log-ins
➕
Intranet integration access to all in your organisation